Unknown Facts About Plastic Manufacturings
Wiki Article
Getting The Die Casting To Work
Table of ContentsRumored Buzz on Manufacturing IndustriesAn Unbiased View of Additive Manufacturing7 Simple Techniques For Lean ProductionManufacturing - The FactsSome Known Factual Statements About Lean Manufacturing
After that, the mould shuts and the procedure repeats. Pre-moulded or machined parts can be placed right into the tooth cavity while the mould is open, enabling the material infused in the next cycle to form and solidify around them. This procedure is referred to as Insert moulding and also allows single components to include multiple products.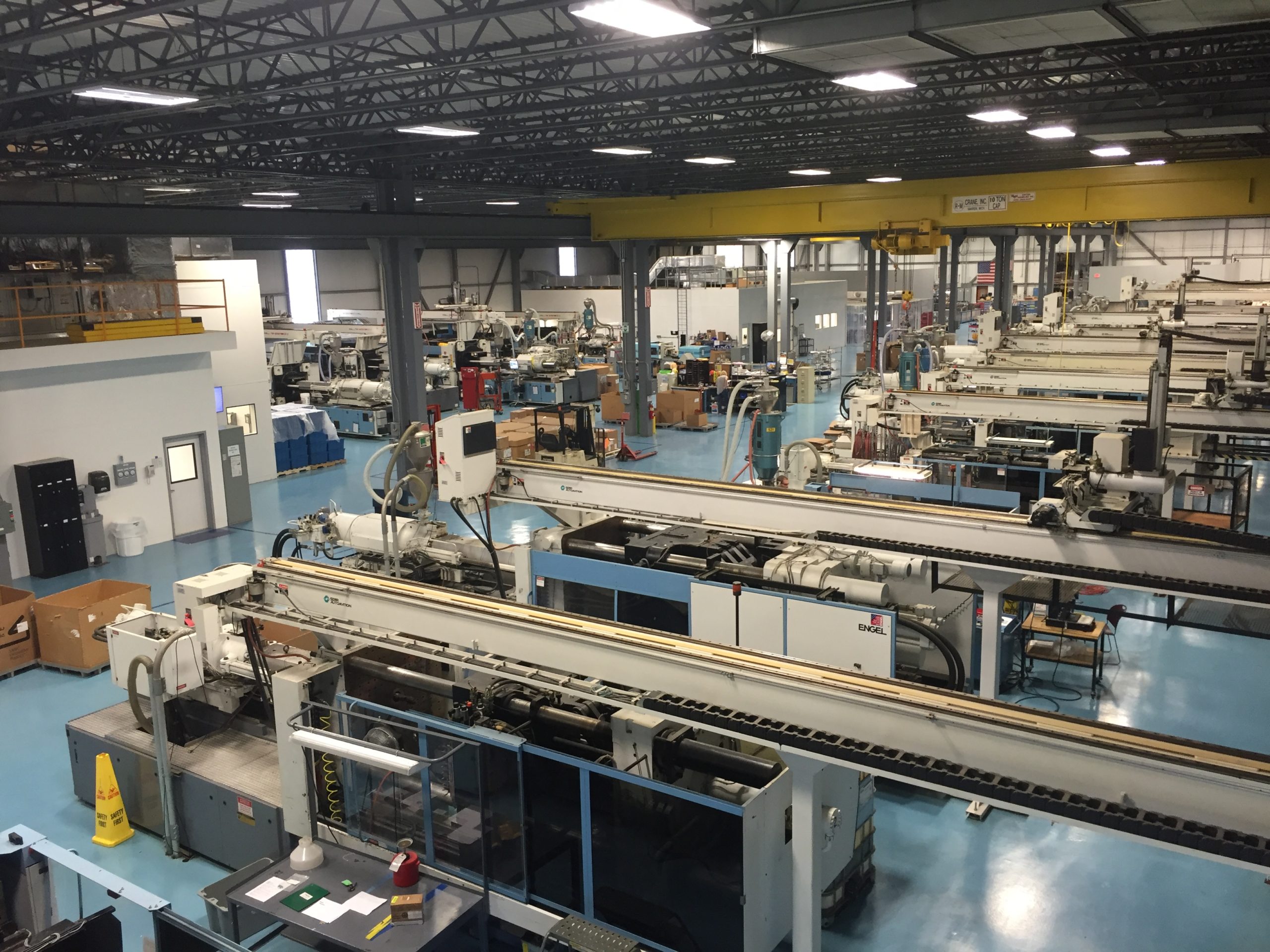
The plastic shot moulding market has evolved over the years from creating combs as well as buttons to generating a large array of products for lots of industries including vehicle, medical, aerospace, consumer items, toys, pipes, packaging, and also construction.: 12 Instances of polymers best suited for the procedure [modify] A lot of polymers, occasionally described as materials, may be utilized, consisting of all thermoplastics, some thermosets, as well as some elastomers.
Offered materials include alloys or blends of previously established products, so item developers can pick the product with the most effective collection of residential or commercial properties from a vast choice. Major standards for choice of a product are the strength and also feature needed for the last part, along with the expense, but additionally each product has various specifications for moulding that must be taken into account.: 6 Various other considerations when selecting a shot moulding material include flexural modulus of elasticity, or the degree to which a product can be bent without damages, in addition to warmth deflection and also water absorption.
The Additive Manufacturing Diaries
Applications include buckles for anchoring and disconnecting outdoor-equipment webbing. Injection moulding equipments are composed of a material receptacle, an injection ram or screw-type plunger, and a home heating unit.: 240 Additionally recognized as platens, they hold the moulds in which the parts are formed. Presses are ranked by tonnage, which shares the amount of clamping force that the equipment can exert.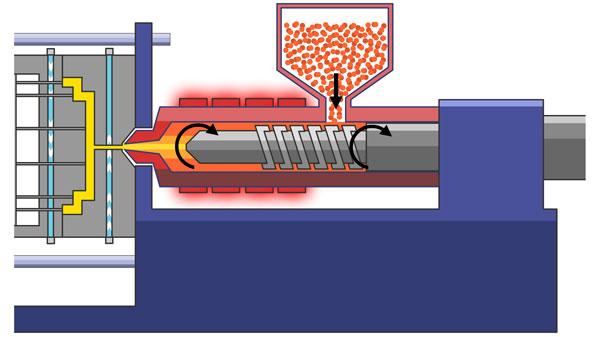
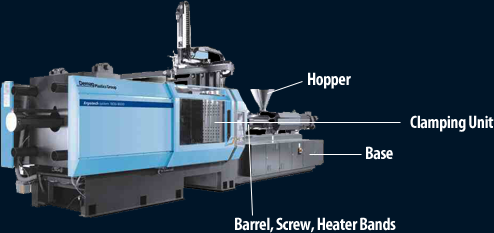
Mould or pass away are the common terms made use of to describe the device made use of to generate plastic components in moulding. Because moulds have been expensive to manufacture, they were typically just utilized in mass production where hundreds of components were being produced. Typical moulds are built from solidified steel, pre-hardened steel, aluminium, and/or beryllium-copper alloy.: 176 The option of material to build a mould from is mostly among business economics; as a whole, steel moulds set you back more to construct, yet their longer lifespan offsets the higher initial price over a higher number of components made before wearing.
Lean Production Fundamentals Explained
Shot moulding die with side draws "A" side of crave 25% glass-filled acetal with 2 side pulls. Shut up of detachable insert in "A" side. "B" side of die with side pull actuators. Mould layout [edit] Typical 2 plates tooling core and tooth cavity are inserts in a mould base "family mould" of 5 various parts The mould consists of 2 key parts, the injection mould (A plate) as well as the ejector mould (B plate).Plastic material enters the mould through a or entrance in the shot mould; the sprue bushing is to secure securely against the nozzle of the injection barrel of the moulding equipment and to enable liquified plastic to flow from the barrel right into the mould, likewise referred to as the cavity.: 141 The sprue bushing routes the liquified plastic to the dental caries photos through networks that are machined right into the faces of the An and B plates.
(A) Sprue, (B)&(C)runner and also (D)gateways in actual injection moulding item for playthings The quantity of resin needed to fill up the sprue, runner and tooth cavities of a mould consists of a "shot". Caught air in the mould can run away via air vents that are ground right into the parting line of the mould, or around ejector pins and also slides that are a little smaller than the openings retaining them.
The air can also come to be so pressed that it sparks and burns the surrounding plastic material.: 147 To permit removal of the moulded part from the mould, the mould functions need to not overhang each other in the instructions that the mould opens, unless parts of the mould are designed to move from between such overhangs when the mould opens up using parts called Lifters.
Lean Manufacturing Things To Know Before You Buy
The coolant soaks up warm from the mould (which has actually absorbed warmth from the hot plastic) and also keeps the mould at an appropriate temperature level to solidify the plastic at the most efficient rate.: 86 To reduce maintenance and venting, cavities and also cores are split into items, called inserts, as well as sub-assemblies, additionally called inserts, blocks, or chase blocks.More complex components are developed using more complex moulds. These may have areas called slides, next that step right jit system into a tooth cavity perpendicular to the draw instructions, to form looming part functions. When the mould is opened, the slides are retreated from the plastic part by making use of stationary "angle pins" on the stationary mould half. oem.
The part is after that expelled as well as the mould shuts. The closing activity of the mould creates the slides to move ahead along the angle pins.: 268 A mould can generate a number of duplicates of the very same parts in a solitary "shot". The number of "impacts" in the mould of that component is commonly improperly referred to as cavitation.
In many cases, numerous tooth cavity tooling moulds a series of various parts in the same device. Some toolmakers call these moulds family members moulds, as all the components are relatede. g., plastic version kits.: 114 Some moulds allow formerly moulded parts to be returned to permit a new plastic layer to create around the initial component.
The Best Strategy To Use For Manufacturing Industries
This system can allow for production of one-piece tires and wheels. Two-shot or multi-shot moulds are made to "overmould" within a single moulding cycle and must be processed on specialised shot moulding equipments with two or even more injection systems. This process is actually an injection moulding procedure performed two times and also as a result has a much smaller sized margin of error.The second material, a various colour, is injection-moulded right into those areas. Pushbuttons and also tricks, for circumstances, made by this procedure have markings that can not click subside, and continue to be legible with hefty use.: 174 Mould storage space [edit] Suppliers most likely to excellent sizes to shield custom-made moulds because of their high standard expenses.
Report this wiki page